Facility
The production facility of ductile iron pipes is a complex and highly specialized operation that requires a combination of advanced technologies, skilled labor, and strict quality control measures to ensure the production of high-quality pipes. By following rigorous production processes, implementing quality control measures, and investing in research and development, the facility can produce ductile iron pipes that meet the highest standards of quality and reliability.
Our production capacity exceeds 100,000 tons per year. As a ductile iron pipe factory, we are equipped with four centrifugal casting machines of various sizes, advanced laboratories for thorough testing at every production stage, three cement mortar lining finishing lines, and a variety of external and internal coatings to meet our customers’ requirements.
- Home
- Facility
Metal Melting & Mg Treatment Section
The melting process must include chemical composition inspections at every stage, including during furnace melting, pouring molten metal into ladles, and subsequent treatment with magnesium. Throughout the melting process, temperature and composition are of paramount importance. Controlled melting ensures the metal reaches the correct temperature and chemical composition. Continuous monitoring through chemical and thermal analysis is conducted to maintain the desired carbon and silicon levels, which are crucial for ductile iron production. Additionally, precise control of the pouring temperature is essential to prevent common defects.
Ductile iron, also known as Spheroidal Graphite (SG) iron or nodular iron, is a type of cast iron that has been treated to improve its properties, particularly its ductility. It is made by adding small amounts of magnesium to molten iron before casting. This magnesium promotes the formation of graphite in the form of discrete nodules rather than the typical flake-like structure found in traditional cast iron. These nodules give ductile iron its unique combination of strength and ductility, making it highly suitable for applications where flexibility and resilience are required, such as in pipe making.
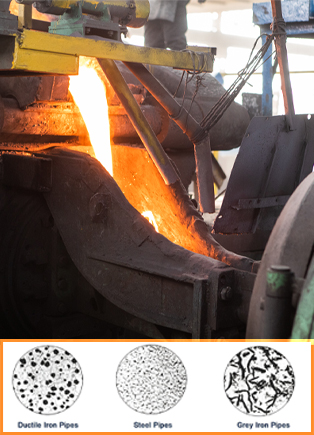
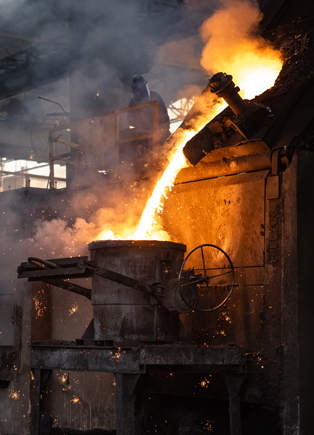
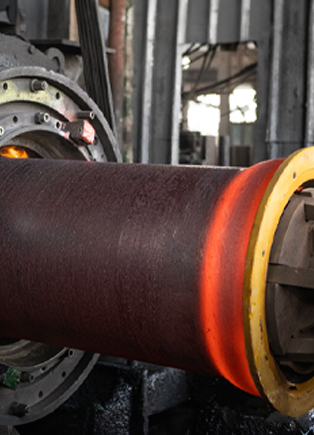
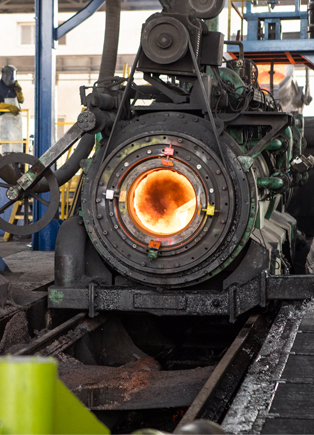
Centrifugal Casting & spinning Section
GCP utilizes roller supporting horizontal cold mold centrifugal casting machines to produce ductile iron (DI) pipes . These machines are equipped with fully automated systems controlled by programmable logic controllers (PLCs). The automated functions include automatic pouring of molten metal, automatic coating of the mold, automatic cleaning of the mold inner wall, and automatic extraction of the cast product.
Centrifugal casting machines are capable of producing DI pipes with lengths up to 6 meters and diameters ranging from 100mm to 1200mm. The water-cooled metal mold process is employed for this purpose, ensuring efficient cooling and solidification of the molten metal to achieve the desired pipe dimensions and properties.
GCP has four centrifugal casting machines with different size capabilities: DN 100 – DN 400, DN 100 – DN 300, DN 300 – DN 700, and DN000 – DN1200
Sand Cores Making Section
The shell core molding process, also known as core creation for forming DI pipe sockets, involves blowing resin-coated sand into a preheated core box. Typically, this box is heated to temperatures ranging between 220 and 235 degrees Celsius. The elevated temperature of the core box facilitates the bonding of sand grains, resulting in the formation of the finished shell core. This core can then be utilized within a die to shape interior contours during casting.
The resultant shell core finds application across various casting processes, enabling the creation of intricate, uniform, and precise interior shapes. Castings produced using this method boast smooth interior surfaces, minimal surface defects, and high dimensional accuracy. Removal of the shell core post-casting is facilitated through heat treatment and other knockout procedures.
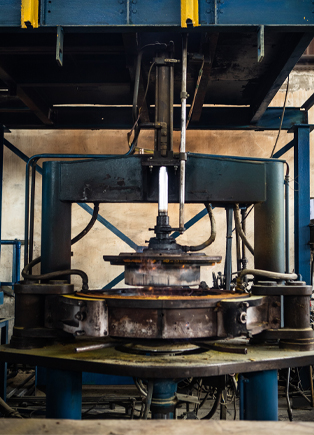
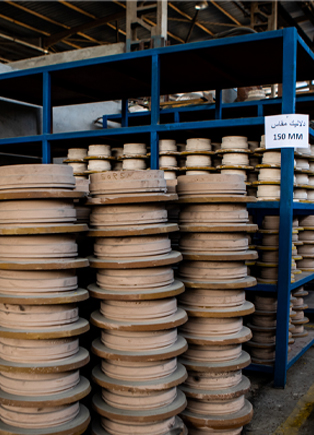
Heat Treatment (Annealing ) Section
In the heat treatment section, the cast pipes undergo annealing in a specialized furnace to enhance their strength and ductility. This annealing furnace is designed as a continuous chain type and operates using gas firing. It consists of distinct zones including a pre-heating section, soaking zone, fast cooling segment, and controlled cooling areas. Initially, pipes enter the pre-heating zone at 600°C and are gradually heated to 940°C. Subsequently, they move into the soaking zone, where they are held at 940°C before transitioning to the fast cooling zone, where they are rapidly cooled to 780°C. Finally, the pipes enter the controlled cooling zone, where they are gradually cooled down to 600°C. Within the annealing furnace, pipes are transported along casting iron rails and propelled by fingers on a closed dog-type chain system.
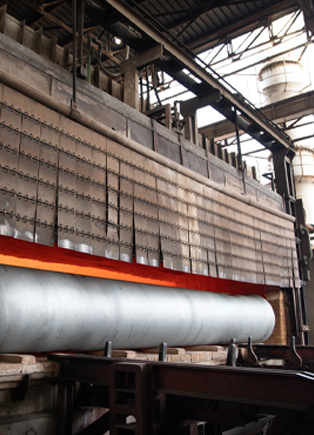
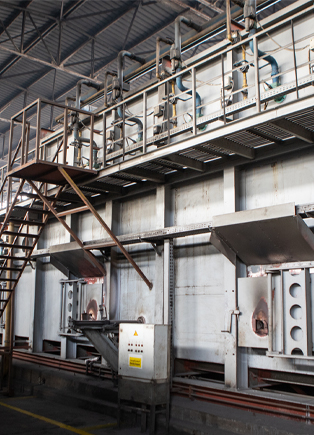
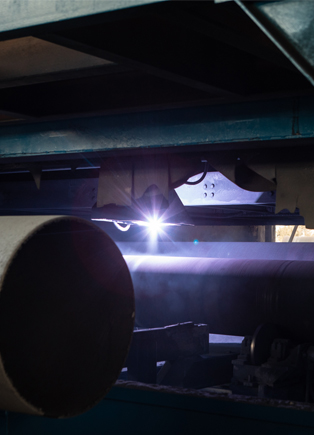
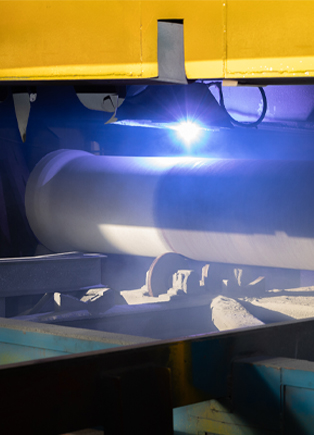
Zinc Coating Section
Zinc coating is applied using a spray process employing Zinc spray guns to ensure consistent and even deposition of Zinc. This coating forms a stable protective layer of insoluble zinc salt, enhancing the pipe’s resistance to corrosion through the galvanizing effect. Prior to zinc application, the pipe surface is meticulously prepared, kept dry, and devoid of rust, non-adhering particles, or foreign substances like oil or grease.
The metallic zinc coating envelops the pipe’s external surface, providing a dense, seamless, and uniform layer. Its uniformity is verified through meticulous inspection processes. The zinc mass should not be less than 200 g/m², and its purity is guaranteed to be at least 99.99%. The final coating layer uniformly covers the entire surface of the metallic zinc layer, devoid of any defects such as bare patches or poor adhesion.
The thickness of the finishing layer remains consistent at 70 microns, with local minimum thickness not less than 50 microns. Additionally, specialized coatings like extra zinc coating can also be applied as per requirements.
Hydrostatic Testing Section
All pipes undergo hydrostatic testing, with the pressure level determined by the size and class of the Ductile Iron Pipe. The pipes are filled with water until completely full and then pressurized to a predetermined value for a fixed duration. During the test, internal pressure is steadily applied and maintained for 10 seconds. Pipes must successfully withstand this pressure without exhibiting any signs of leakage, sweating, or other defects.
A total of 23 m³/hr of water is circulated for this process. The water utilized for hydro-testing is recirculated after settling in settling tanks, which is included in this section. Approximately 19 m³/hr of water is reclaimed from the settling tank, with an additional 1 m³/hr required as makeup water.
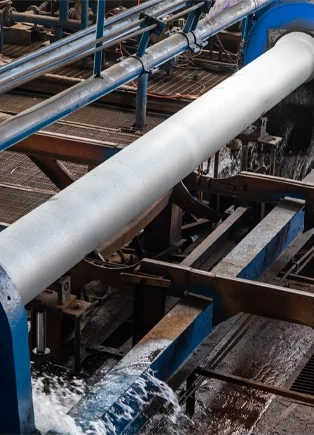
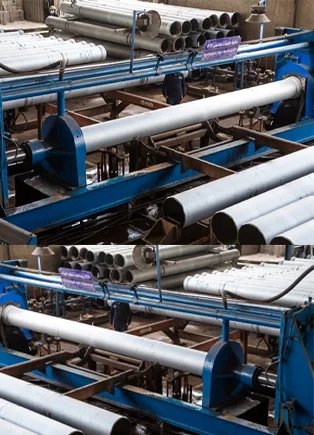
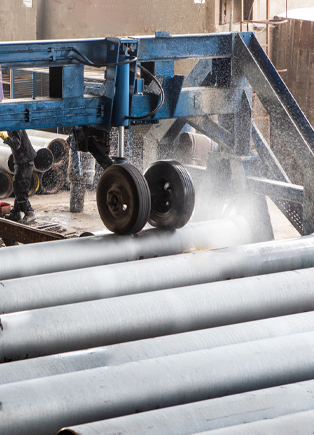
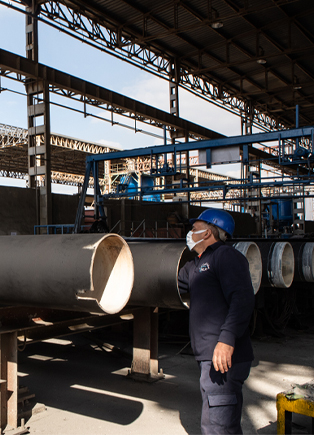
Cement Mortar Lining Section
All Ductile Iron Pipes come equipped with internal cement mortar lining, ensuring enhanced durability. The mortar composition must adhere to a ratio of at least 1 part cement to 3.5 parts sand by mass (i.e., S/C ≤ 3.5 by mass in the mortar). Lining thickness varies according to pipe size: 3 mm for DN 80 – DN 300, 5 mm for DN 350 – DN 600, and 6 mm for DN 700 – DN 1200 pipes.
The equipment essential for cement lining of pipes includes batching, mixing, and material transfer machinery, alongside cement and sand silos, as well as a cement lining machine equipped with traversing equipment. Internally lined Ductile Iron Pipes undergo curing in a dedicated curing oven. Additionally, specialized linings such as CML with Bitumen Seal Coat and CML with Epoxy Coat are also available options.
Bituminous Coating Section
The pipes undergo preheating in a hot chamber to eliminate any residual moisture from steam curing and to ensure optimal adhesion for subsequent painting. Bituminous paint is then applied using a spraying machine, ensuring a uniform coating across the surface of the Ductile Iron Pipe. The coating process is conducted on a clean surface, devoid of any moisture or dust, to ensure smooth and robust adhesion.
The applied coating must possess specific properties: it should be sufficiently hard to resist flow when exposed to temperatures of 65°C, yet not excessively brittle at 0°C to prevent chipping when marked with a penknife. The average thickness of the coating should not be less than 70 μm, with local minimum thicknesses not falling below 50 μm. For areas with corrosive soil conditions, additional bituminous coating may be applied as necessary
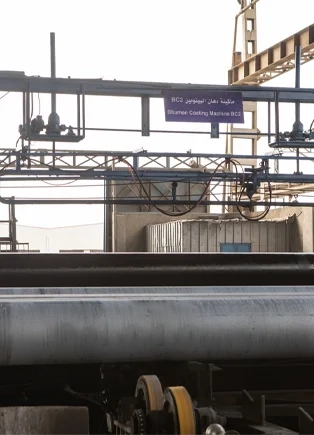
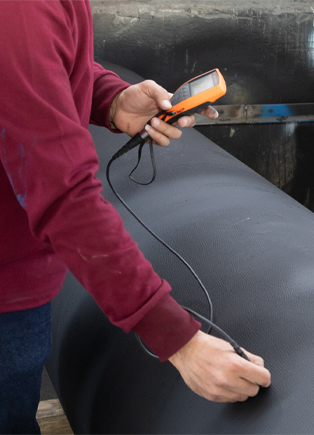
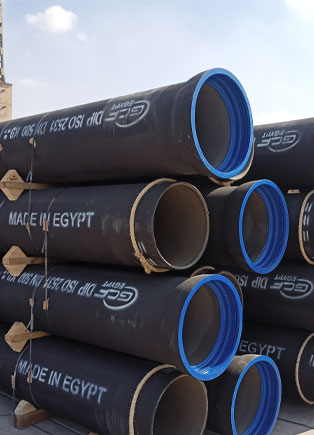
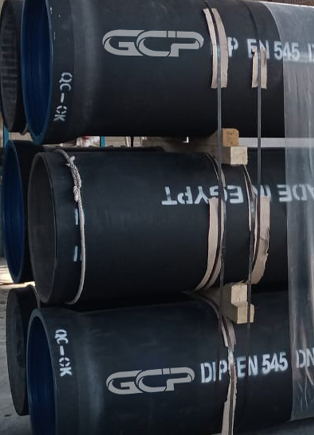
Marking Section
Each pipe must bear durable and clear markings, including but not limited to:
a. A reference to the relevant International Standard, ISO 2531.
b. The manufacturer’s name or trademark.
c. The year of manufacture for identification purposes.
d. Identification as ductile iron.
e. The nominal diameter (DN) of the pipe.
f. The pressure class (C) of socket and spigot pipes.
These markings ensure traceability, compliance, and proper identification of the pipes according to international standards.
Storage and Transportation Section
Transportation & Handling
Ductile iron pipes are strong enough to resist damage during road transportation or handling by cranes or forklifts in seaports and at site. The superior properties of DI Pipes can withstand a toughest of storage conditions without any damages.
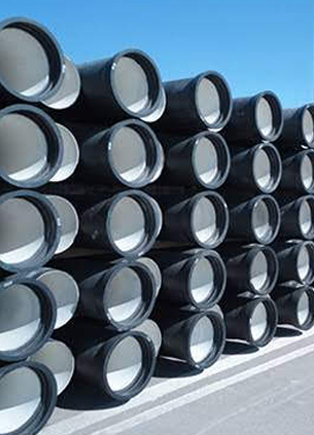
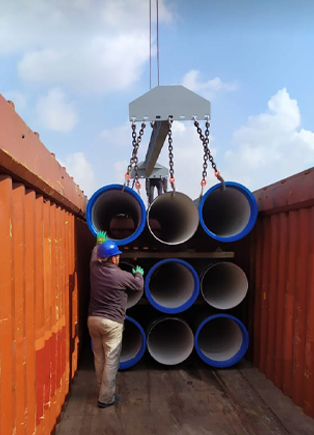
Process Flow Chart
Raw material – Molten iron (composition adjustment in electric furnace) – Spheroidization – Centrifugal casting – Heat Treatment (Annealing) – Zinc coating – Hydraulic testing – Cement mortar lining (curing/polishing) – External finishing coating and marking – Packing and storage – Shipping to port for Delivery.
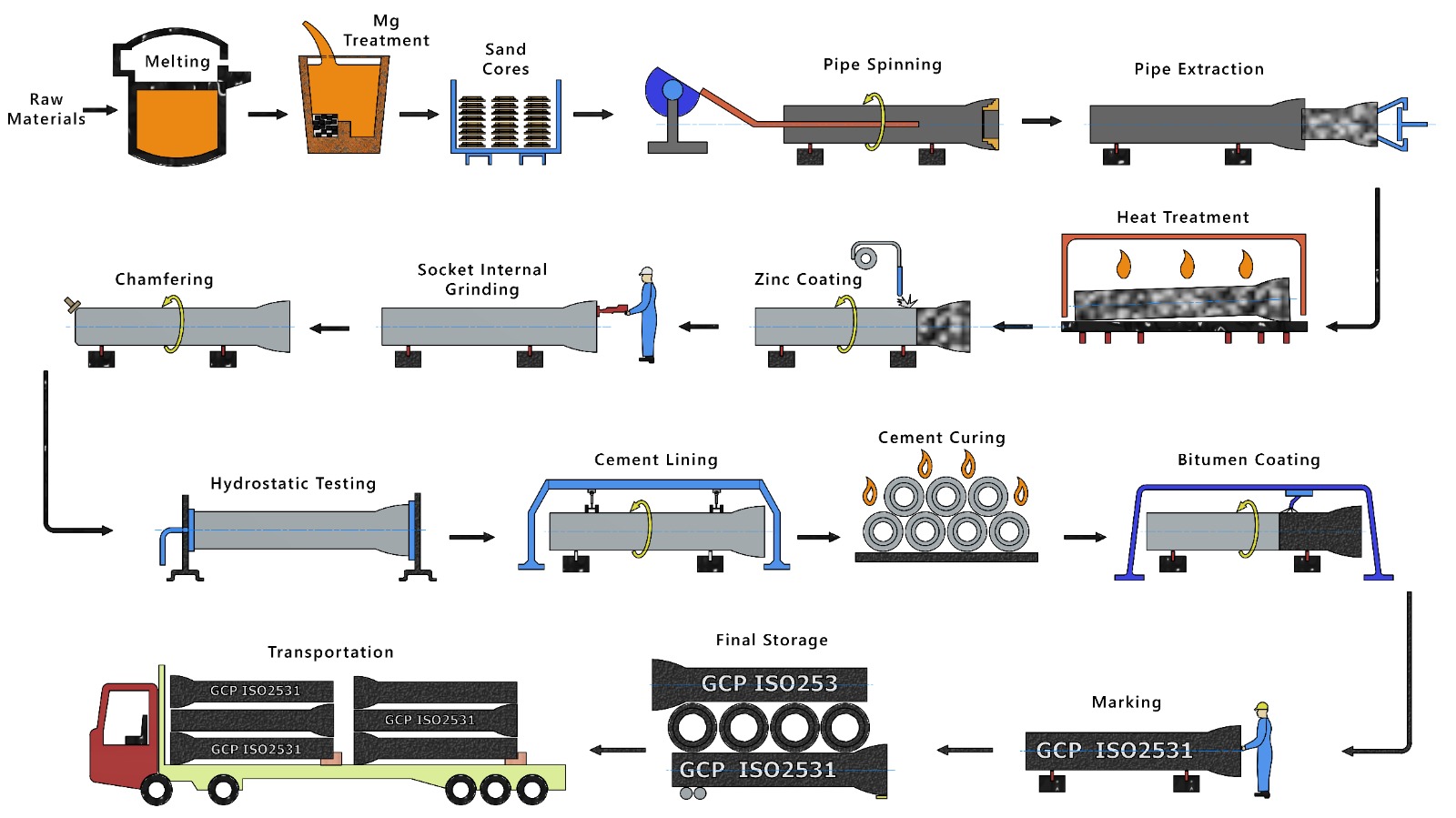