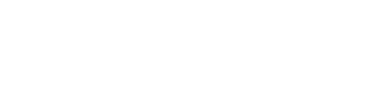
We connect
and sustain communities.
GCP one of the leading manufacturer of DI pipes in MEA Region
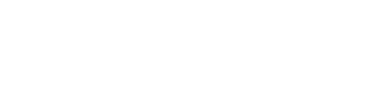
Testing, Process Control, and compliance with the QM System.
Our diverse portfolio represents decades of manufacturing experience backed by a passion for quality, outstanding client service and the latest industry.
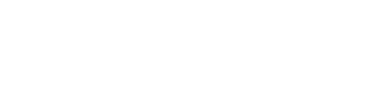
Quality Control . Honest Service. Great Value.
Our diverse portfolio represents decades of manufacturing experience backed by a passion for quality, outstanding client service and the latest industry.
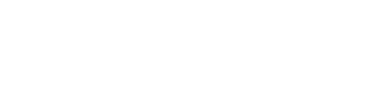
We build your
Projects with trust.
Our diverse portfolio represents decades of construction experience backed by a passion for quality, outstanding client service and the latest industry.
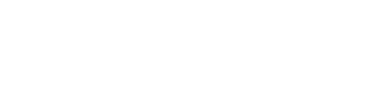
We connect
and sustain communities.
GCP one of the leading manufacturer of DI pipes in MEA Region
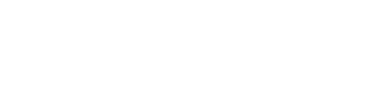
Testing, Process Control, and compliance with the QM System.
Our diverse portfolio represents decades of manufacturing experience backed by a passion for quality, outstanding client service and the latest industry.
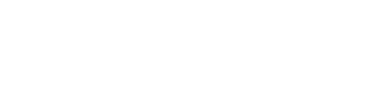
Quality Control . Honest Service. Great Value.
Our diverse portfolio represents decades of manufacturing experience backed by a passion for quality, outstanding client service and the latest industry.
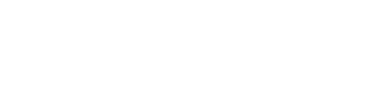
We build your
Projects with trust.
Our diverse portfolio represents decades of construction experience backed by a passion for quality, outstanding client service and the latest industry.
“We understand our customers’ need for a consistent and reliable supply of DI pipes. To fulfill this requirement, our Quality Assurance strategies focus on three primary areas: Testing, Statistical Process Control, and compliance with the Quality Management System in accordance with ISO 9001:2015 standards.”
Quality control in the ductile iron pipe casting process goes beyond simple testing and inspections; it involves continuous process improvement. Regular process audits, employee training, and technological investments are all essential elements in maintaining high-quality standards throughout the ductile iron pipe manufacturing process.
Our inspectors are skilled in performing a range of both destructive and non-destructive tests to ensure that all components comply with the relevant international, industry, or customer-specific quality standards.
Applied Specification Standards
- Ductile Iron Pipes: EN545, ISO2531
- Push-on gasket: EN681-1, ISO 4633
- Cement lining: EN545, ISO4179
- Dimension of socket and spigots: EN545
- Zinc coating: EN545, ISO 8179
- Bitumen coating: EN545
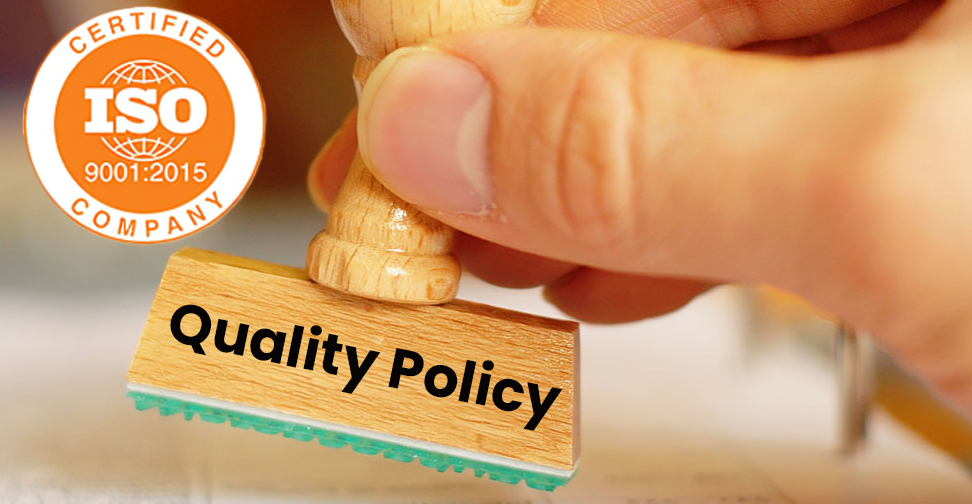
Quality Policy
We are GCP, a top manufacturer of ductile iron pipes for drinking water and sewage systems in the Middle East and Africa. We are committed to a quality management system that aligns with our core values and enables us to deliver superior quality. Our goal is to produce and provide high-quality pipes at competitive prices, serving companies and projects in the infrastructure sector.
GCP’s management has established a quality policy that aligns with the company’s strategic plans and direction. The top management is dedicated to the effective and efficient implementation of the quality management system, as well as to continuous improvement and development in accordance with the requirements of the international standard ISO 9001:2015.

Raw Material Receiving QC Process
GCP firmly believes that Quality Control is the cornerstone of producing flawless Ductile Iron Pipes. Quality control measures are integrated at every stage of production, from the inspection and acceptance of raw materials to the final evaluation of the finished DI pipes.
The quality control process begins with a thorough examination of raw materials. Iron and alloying elements must meet precise chemical compositions to ensure the desired properties in the final product. Although suppliers typically provide material certificates, additional testing methods such as spectrometry may be used for verification.
HIGH QUALITY (SELECTIVE) Steel Scrap
We inspect the physical properties of steel scrap sheet metal to ensure it meets specific criteria: it must be dry, free of grease or contaminants, free from deep rust, non-galvanized, and its chemical composition must comply with GCP internal specifications. If these standards are not met, the material is returned to the suppliers.
The following QC check steps shall be applied
- Physical check of properties of steel scrap sheet (Visual Inspection 100%)
- Chemical Analysis Sample (with spectrometer)
Metal Melting QC Process
The melting process must include chemical composition inspections at every stage, including during furnace melting, pouring molten metal into ladles, and subsequent treatment with magnesium. Throughout the melting process, temperature and composition are of paramount importance. Controlled melting ensures the metal reaches the correct temperature and chemical composition. Continuous monitoring through chemical and thermal analysis is conducted to maintain the desired carbon and silicon levels, which are crucial for ductile iron production. Additionally, precise control of the pouring temperature is essential to prevent common defects.
The following QC check steps shall be applied
- Chemical Analysis Sample from Furnace (Every Furnace Treatment) (with spectrometer)
- Chemical Analysis Sample from Ladle (One Sample/ Ladle) (with spectrometer)
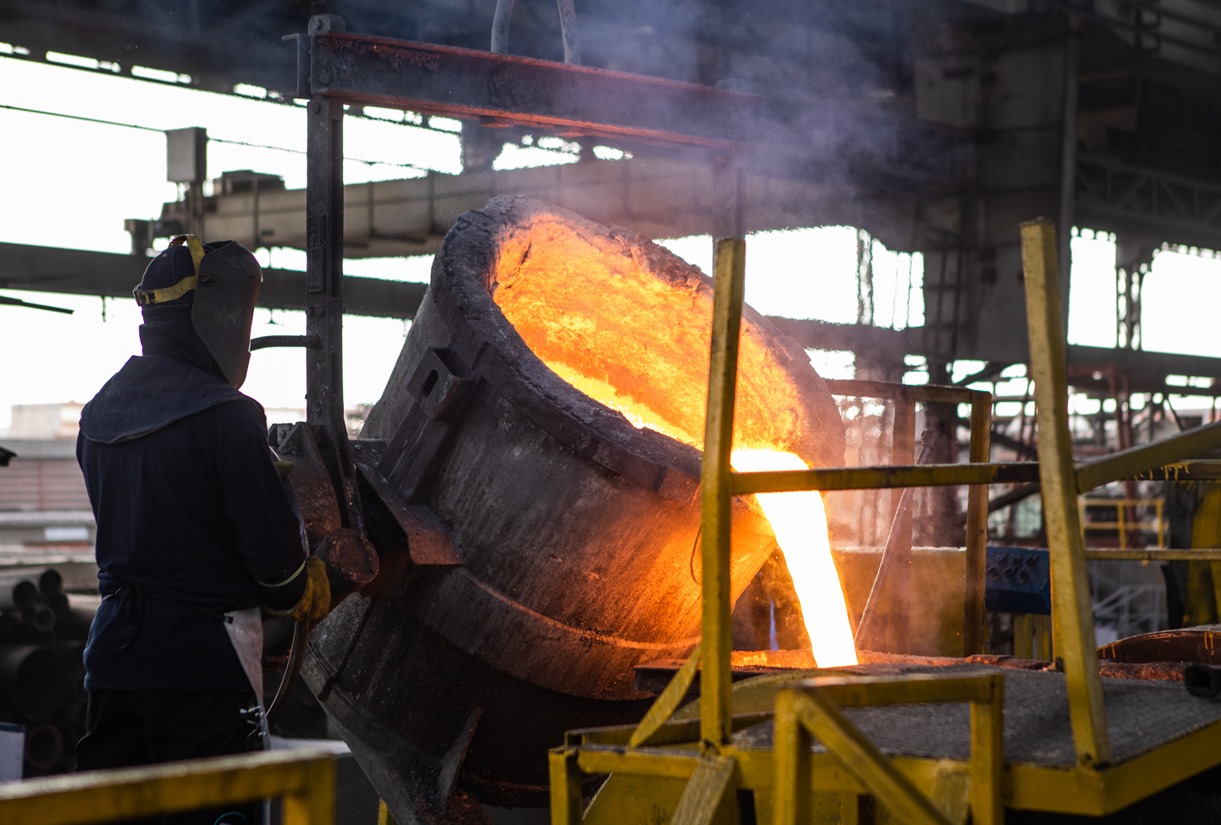
Pipe Casting QC Process
Ductile Iron Pipes are casted in steel molds that are rotated at high speed before molten ductile iron is poured in. The centrifugal force generated by the spinning mold ensures even distribution of the material along the inside surface. After the ductile iron has cooled adequately, the pipe can be extracted from the mold for subsequent processing.
The following QC check steps shall be applied
- Surface Defects Check, Visual Inspection (100%)
- Wall Thickness Check (100% with Pistol Caliper, and 3 Pipes/Shift Metal Ultrasonic Device)
- Weight Check (100% with Digital Weighing Scale)
- Ovality Check (8 Sample/ Shift with Go No Go Gauge)
- Straightness Check (100%)
- Length Check (100%)
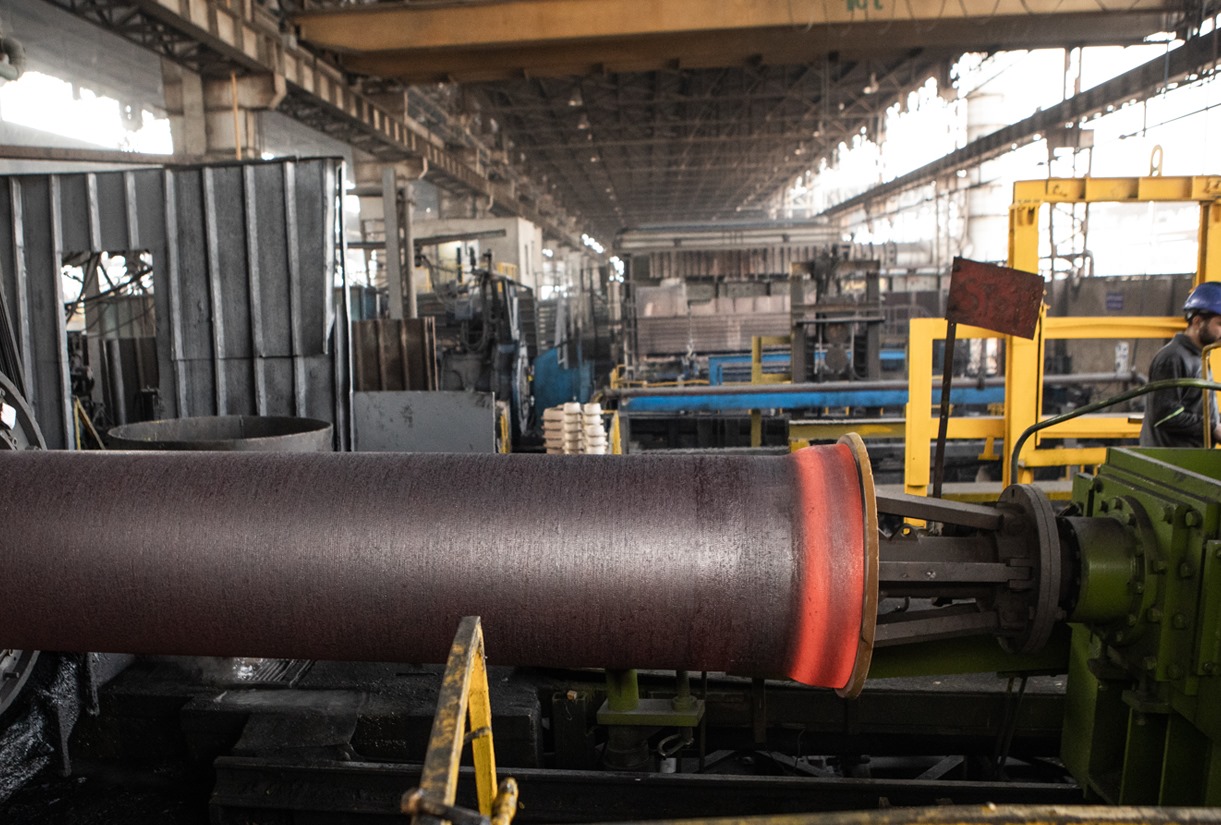
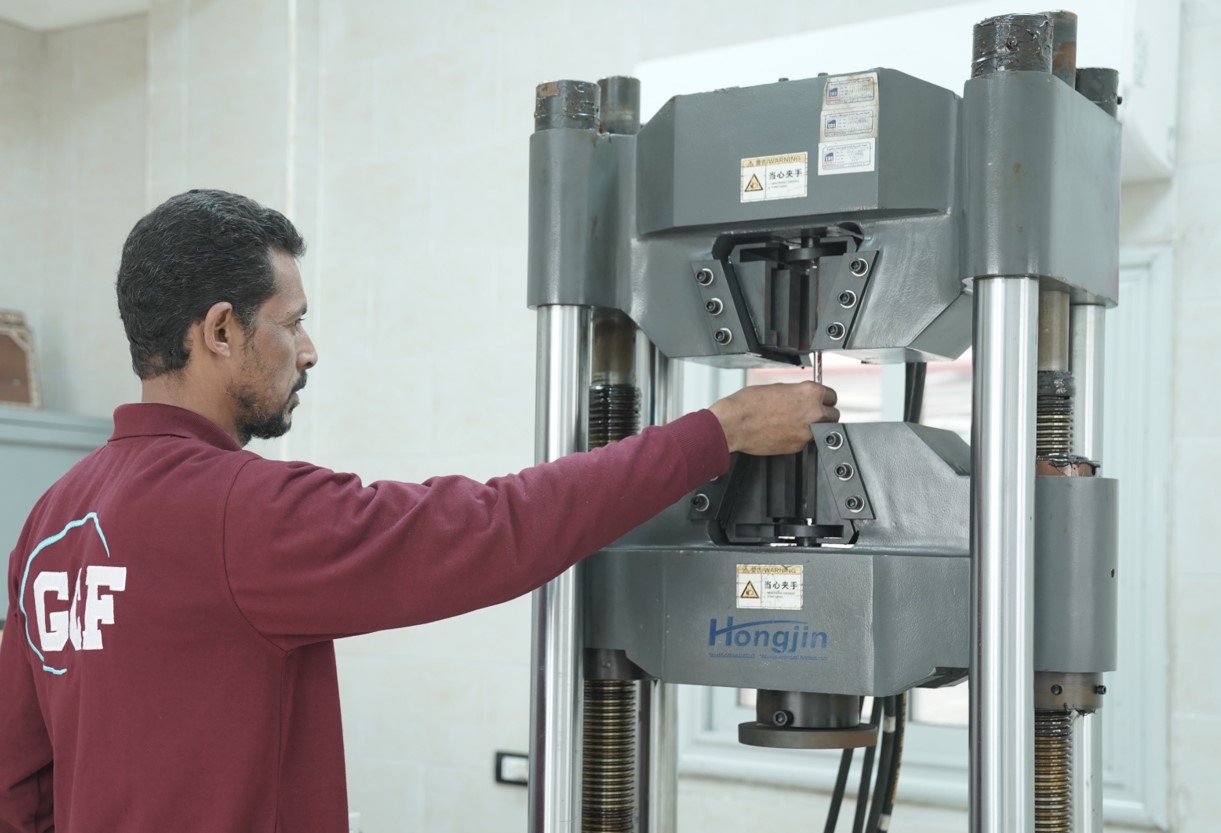
Heat Treatment QC Process
The Horizontal Continuous Annealing Furnace has a processing capacity ranging from DN80 to DN1200. Cast pipes undergo heat treatment in this furnace to enhance their strength, resilience, and ductility. The improved mechanical properties result from a combination of factors, including the chemical composition of iron and high-temperature annealing. This process enables the pipes to withstand alternating loads, earth movement, and sagging, ensuring their suitability for various applications.
The following QC check steps shall be applied
- Tensile Strength Test (Last Sample/ Ladle (Normal) & 100% of ladle (Special)
- Elongation Test (Last Sample/ Ladle (Normal) & 100% of ladle (Special)
- Brinell Hardness Test 3 Sample/ Shift
- Microstructure Check (Last Sample/ Ladle (Normal) & 100% of ladle (Special)
- Ring Test Any pipe don’t test (tensile+ microstructure), Ring Test Machine
Zinc Coating QC Process
The standard coating for GCP ductile iron pipes comprises a layer of sprayed metallic zinc with a minimum thickness of 200 g/m2, which is then covered with bituminous paint. This coating is considered active and is suitable for a wide range of soil conditions. The zinc coating provides active protection through the galvanic action of the zinc/iron couple, offering dual mechanisms for corrosion resistance.
The following QC check steps shall be applied
- Surface Inspection Before Coating (100% Visual Inspection)
- Measure Zinc Mass Deposition (by 3m Strip After Coating) – 1/Size/Shift
- Surface Inspection After Coating (100% Visual Inspection
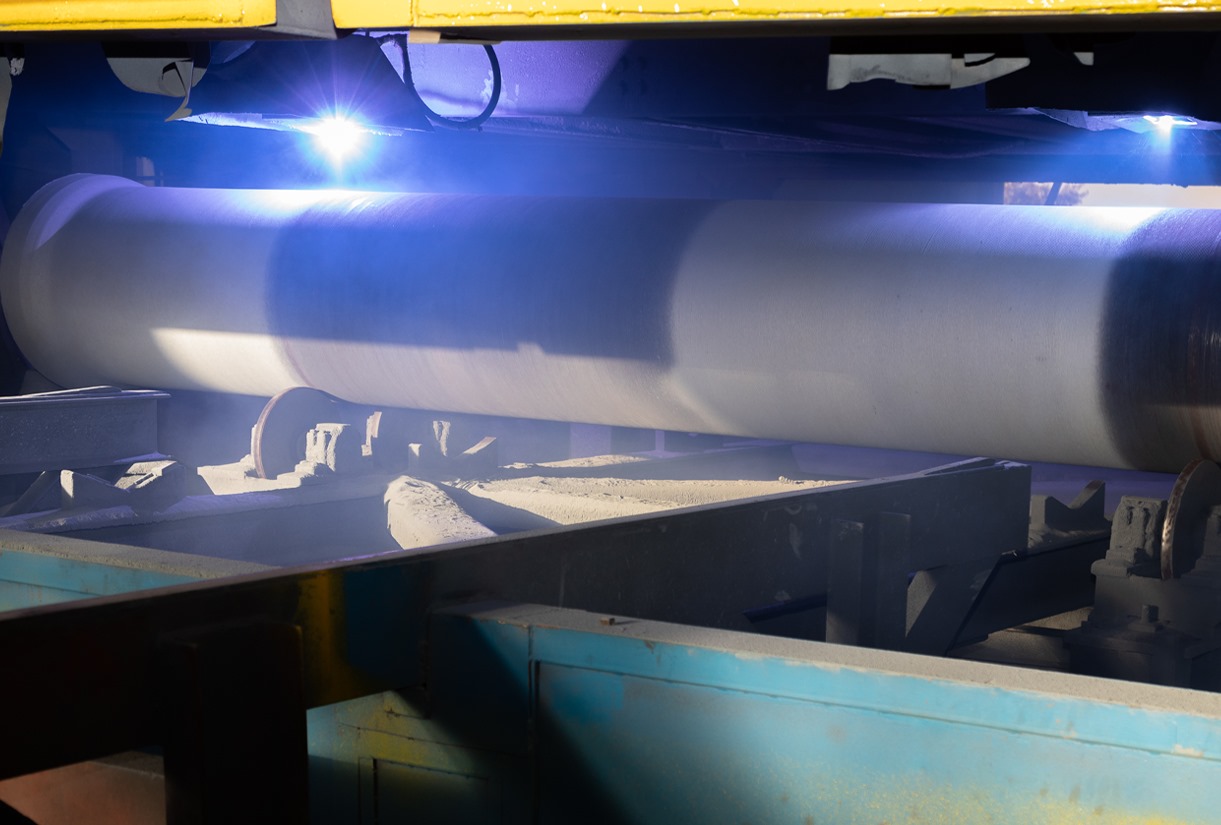
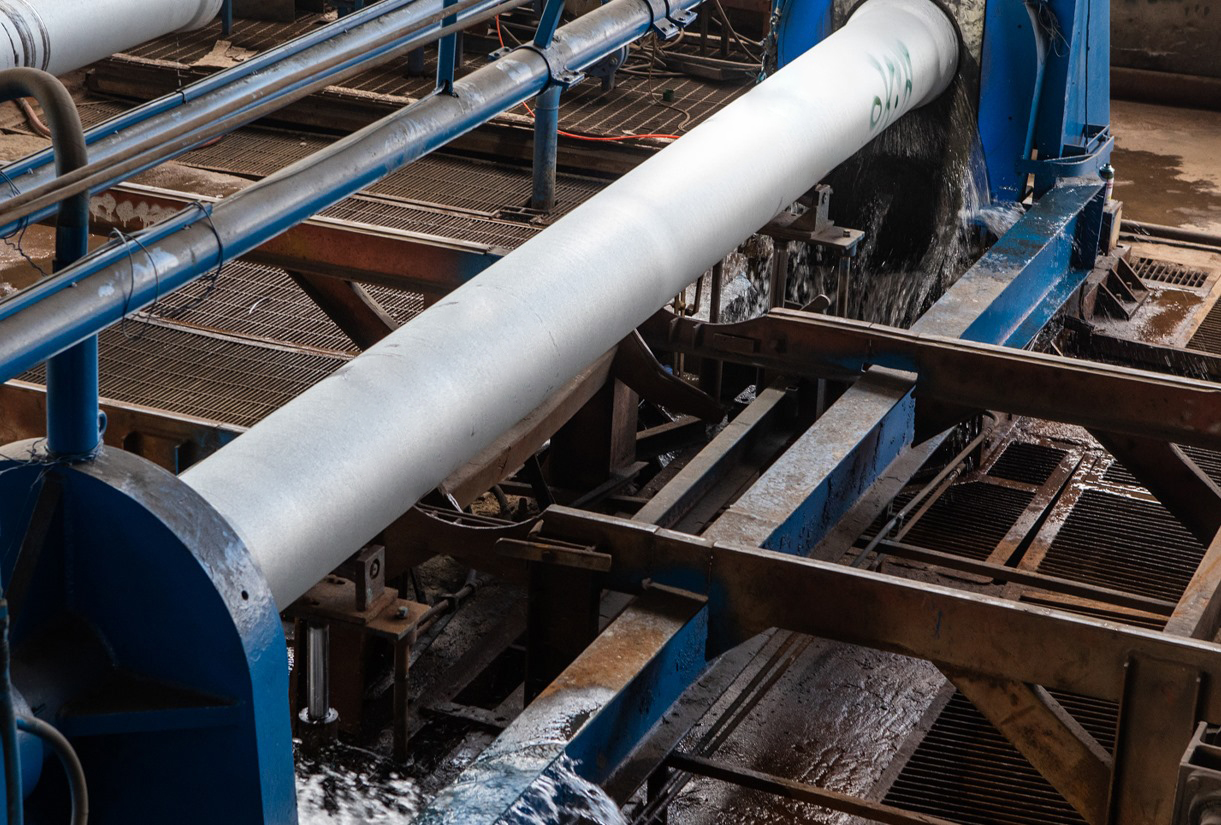
Hydrostatic Testing QC Process
All ductile iron pipes undergo hydrostatic testing, where the pressure is determined by both the size and class of the pipe. The testing process involves filling the pipes with water until they reach full capacity, after which they are pressurized to a predetermined value for a fixed duration of time. This rigorous testing ensures that the pipes meet the required standards for strength and durability, regardless of their size or class.
The following QC check steps shall be applied
- Hydrostatic Pressure Testing (100%) with Hydrostatic Pressure Testing Machine
Cement Mortar Lining QC Process
The centrifugal process of applying mortar inside a Ductile Iron Pipe involves distributing the mortar evenly throughout the pipe’s length using a moving mechanism while the pipe spins at a relatively low speed. All Ductile Iron Pipes come with internal cement mortar lining, which is formulated to contain at least 1 part cement to 3.5 parts sand by mass (i.e., S/C ≤ 3.5 by mass in the mortar). The lining thickness varies: it is 3 mm for DN 80 – DN 300 pipes, 5 mm for DN 350 – DN 600 pipes, and 6 mm for DN 700 – DN 1200 pipes. This meticulous process ensures consistent and reliable lining for optimal performance of the pipes.
The following QC check steps shall be applied
- Visual Inspection Before Lining (100% Visual Inspection)
- Mortar Application Parameters (One Sample/ Size/ Shift with UT Machine)
- Wet Cement Thickness Inspection (100% Cement Ultrasonic Device and Steel Pin
- Visual Inspection After Lining curing (100% Visual Inspection)
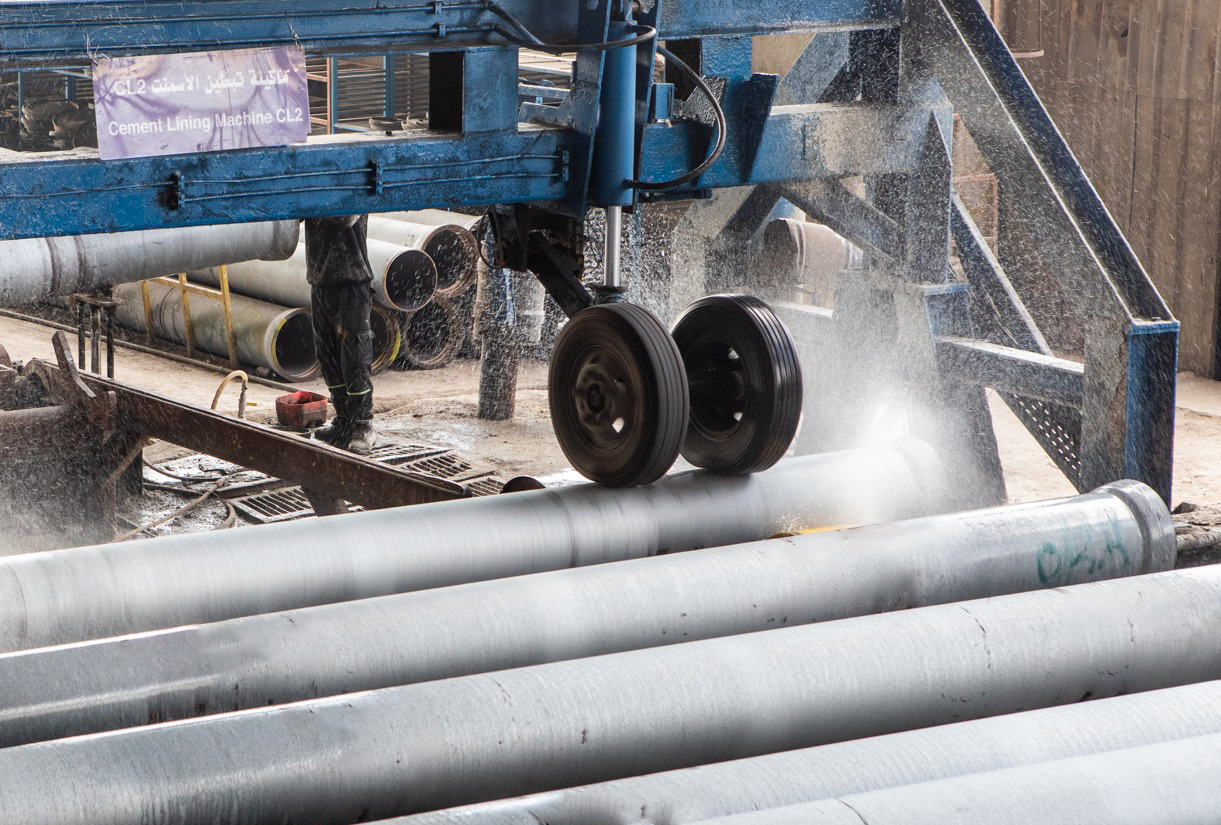
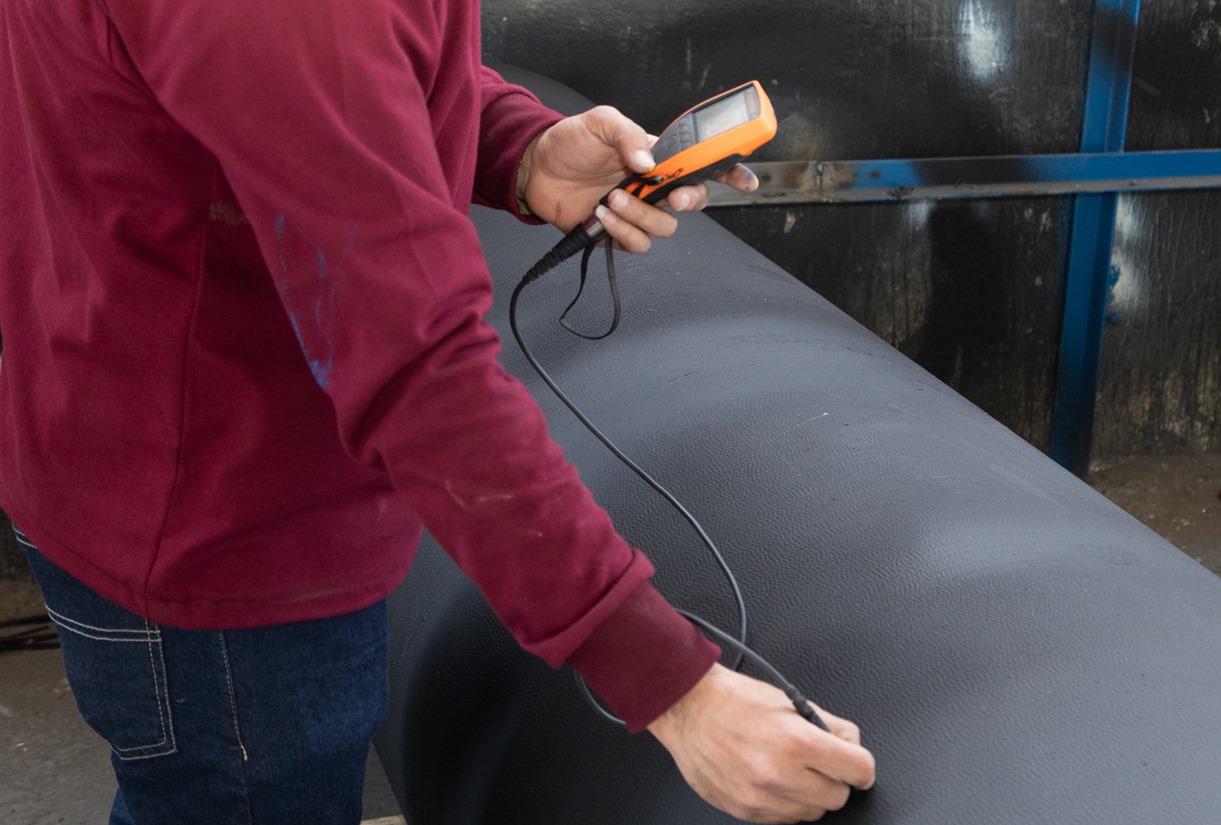
Bitumen / Epoxy coating QC Process
The standard coating for the pipes consists of a combination of metallic zinc and bitumen. This dual-layer coating, comprising a metallic zinc layer followed by a bitumen layer, offers robust protection against a wide range of soil conditions. The application of bituminous paint is carried out using a spraying machine, ensuring a uniform coating across the entire surface of the Ductile Iron Pipe. This meticulous coating process enhances the durability and longevity of the pipes, making them suitable for various environmental conditions.
The following QC check steps shall be applied
- Visual Inspection Before Coating (100% Visual Inspection)
- Coating Thickness Inspection One Sample/ Size/ Shift with Coat meter Device
- Visual Inspection After Coating (100% Visual Inspection)
Marking
All pipes and fittings shall be durably and legibly marked and shall bear at least the following indications: International Standard, ISO 2531, manufacturer’s name or mark, Identification of the year of manufacture, Identification as ductile iron, The DN, The C pressure class of socket and spigot pipe.
The following QC check steps shall be applied
- External Coating Check (100% Visual Inspection)
- Internal Coating Check (100% Visual Inspection)
- Ovality Check (100% Visual Inspection)
- Marking Check (100% Visual Inspection
Quality Control Flow Chart
Raw material – Molten iron (composition adjustment in electric furnace) – Spheroidization – Centrifugal casting – Heat Treatment (Annealing) – Zinc coating – Hydraulic testing – Cement mortar lining (curing/polishing) – External finishing coating and marking – Packing and storage – Shipping to port for Delivery.
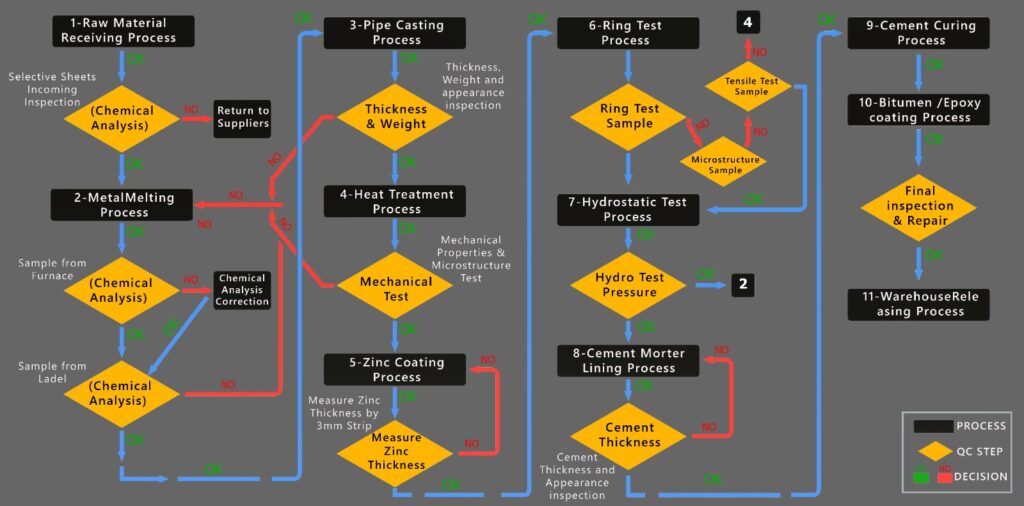